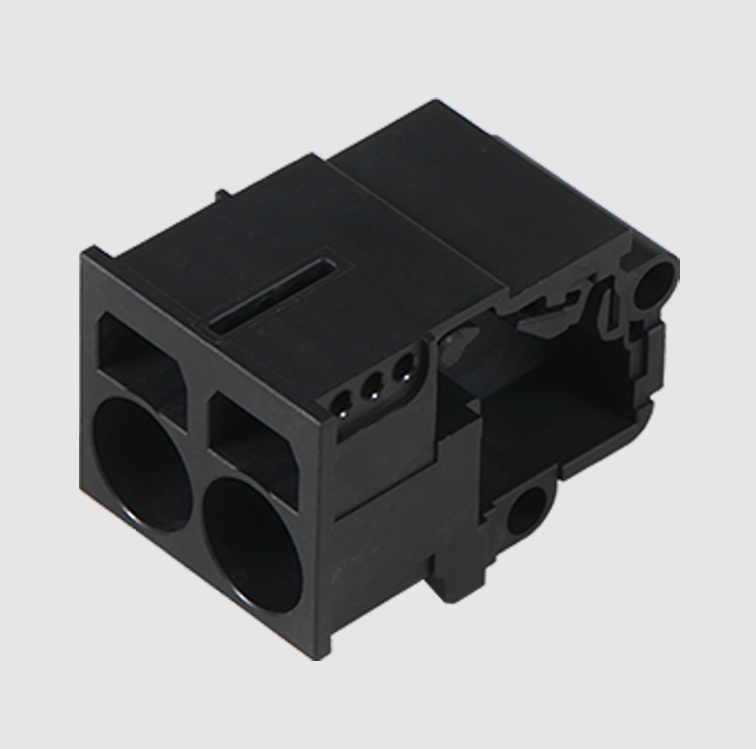
In a major stride forward for the electronics industry, a pilot Connector Components manufacturer has announced the implementation of Customized Production Moulds in their production process. This innovative approach is expected to significantly enhance the efficiency, precision, and customization capabilities of the company's operations, setting a new standard for connector component manufacturing.
The introduction of Customized Production Moulds represents a significant investment in technology and innovation for the company, which has long been at the forefront of connector component production. These moulds are tailor-made to accommodate the unique specifications and requirements of each client, ensuring that the final product meets the high standards of quality and performance.
"The adoption of Customized Production Moulds is a strategic move that aligns with our commitment to delivering high-quality, precision-engineered connector components," said the company's CEO. "By investing in this technology, we are not only improving our production capabilities but also strengthening our position as a pilot global supplier of connector components."
The Customized Production Moulds are designed to accommodate a wide range of connector types, including but not limited to USB, HDMI, and RJ45 connectors. Each mould is meticulously crafted to ensure that the connector components produced are not only functionally predominant but also aesthetically pleasing, meeting the stringent requirements of the electronics industry.
One of the key benefits of using Customized Production Moulds is the increased flexibility they offer in terms of production. The company can now quickly adapt to changing market demands and customer specifications, reducing lead times and improving responsiveness. This agility is critical in an industry where technological advancements are made at a rapid pace, and the ability to stay ahead of the curve is essential for success.
In addition to the operational benefits, the use of Customized Production Moulds also has environmental implications. The precision engineering of these moulds reduces material waste during the production process, pilot to a more sustainable manufacturing process. This aligns with the growing global trend towards eco-friendly practices and the company's commitment to environmental responsibility.
The company's engineering team has been working tirelessly to superb the design and functionality of the Customized Production Moulds. They have conducted extensive research and development, ensuring that the moulds can withstand the rigors of high-volume production while maintaining the integrity of the connector components.
"The development of our Customized Production Moulds has been a labor of love for our team," said the company's Chief Engineer. "We have poured our expertise and passion into creating moulds that not only meet but exceed industry standards. The result is a product that we are incredibly proud of and one that we believe will set a new benchmark for connector component manufacturing."
The company's clients have already begun to reap the benefits of the Customized Production Moulds. Early feedback has been overwhelmingly positive, with clients citing improved product quality, reduced production times, and greater flexibility in terms of customization options.
The adoption of Customized Production Moulds by this Connector Components manufacturer is a significant milestone in the industry. It represents a commitment to innovation, quality, and customer service that is sure to set a precedent for other manufacturers to follow. As the company continues to push the boundaries of what is possible with connector components, the use of Customized Production Moulds will undoubtedly play a crucial role in shaping the future of the electronics industry.