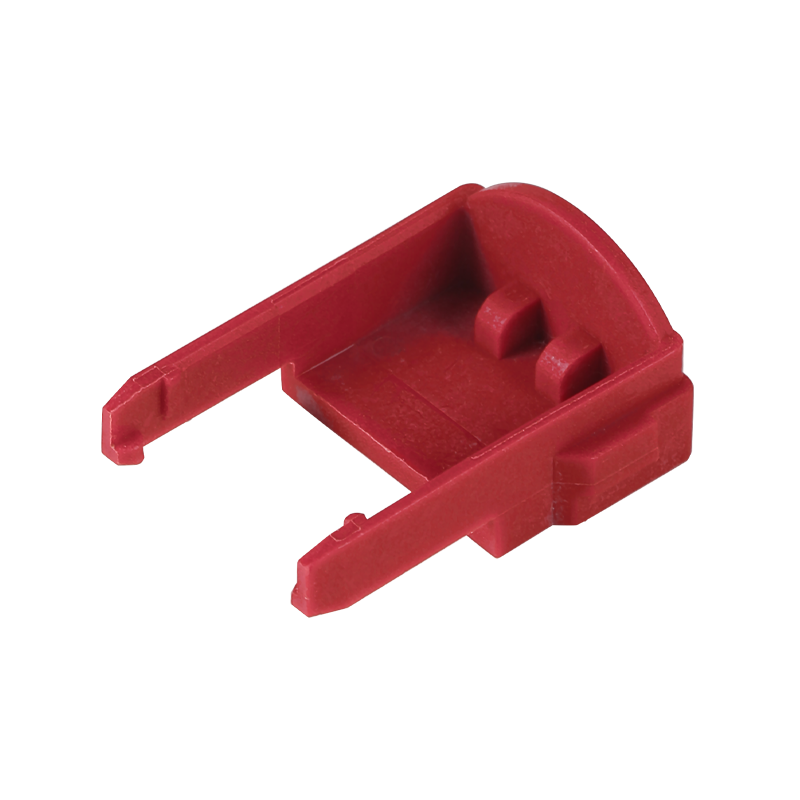
Connector components are essential elements in various electrical systems, providing a reliable and secure means of connecting different parts of a circuit. These components come in a variety of designs and materials, each suited to specific applications. Their main function is to ensure that electrical signals or power are transmitted without interruption or loss, which is crucial in a wide range of industries, from telecommunications to automotive.
One of the more common types of connector components is the pin and socket. This design involves a male pin fitting into a female socket, allowing for easy connection and disconnection of components. Pin and socket connectors are widely used in situations where components need to be regularly removed or replaced, such as in computers and other electronic devices. The materials used for these connectors are typically metals like copper or brass, chosen for their good conductivity and durability.
Another important type of connector component is the terminal block. Terminal blocks are used to connect wires to electrical equipment, allowing for safe and organized connections. These components are commonly found in industrial settings, where large quantities of wiring need to be connected to machinery or control panels. Terminal blocks can be designed to accommodate different wire sizes and configurations, making them versatile for various applications.
In addition to these, there are also circular connectors, which are used in applications where the connection needs to be more robust and capable of withstanding harsher environments. Circular connectors are often found in automotive, aerospace, and military applications, where reliability and durability are essential. These connectors are typically sealed to prevent water, dust, or other environmental factors from interfering with the electrical connection. The contacts within circular connectors are designed to handle high currents, ensuring that the components can work efficiently under load.
The material choice for connector components is critical to their performance. more connectors are made from metals like copper, brass, or aluminum, which offer good electrical conductivity. Additionally, many connectors feature insulating materials like plastic, rubber, or ceramics to prevent short circuits and protect users from electrical shocks. The design of the component, including the number of pins, the size of the connector, and the arrangement of the contacts, can vary depending on the application’s requirements.
Connector components are often designed to meet specific industry standards and certifications, ensuring that they perform reliably under various conditions. These standards address factors such as temperature tolerance, resistance to corrosion, and compatibility with other components. For example, in automotive applications, connectors are designed to withstand vibration, high temperatures, and exposure to chemicals. In contrast, connectors used in consumer electronics may prioritize compact size and ease of use.
The manufacturing process of connector components typically involves precision engineering to ensure that each piece fits goodly within the system. Automated processes such as injection molding and stamping are commonly used to create the intricate designs needed for connectors. These processes allow for mass production of components that are both affordable and reliable.
Connector components play a vital role in the functionality of electrical systems across numerous industries. Their various designs and materials ensure that they can meet the specific needs of different applications, from everyday consumer electronics to complex industrial machinery. Their continued development is essential as technology advances and the need for efficient, reliable connections grows.