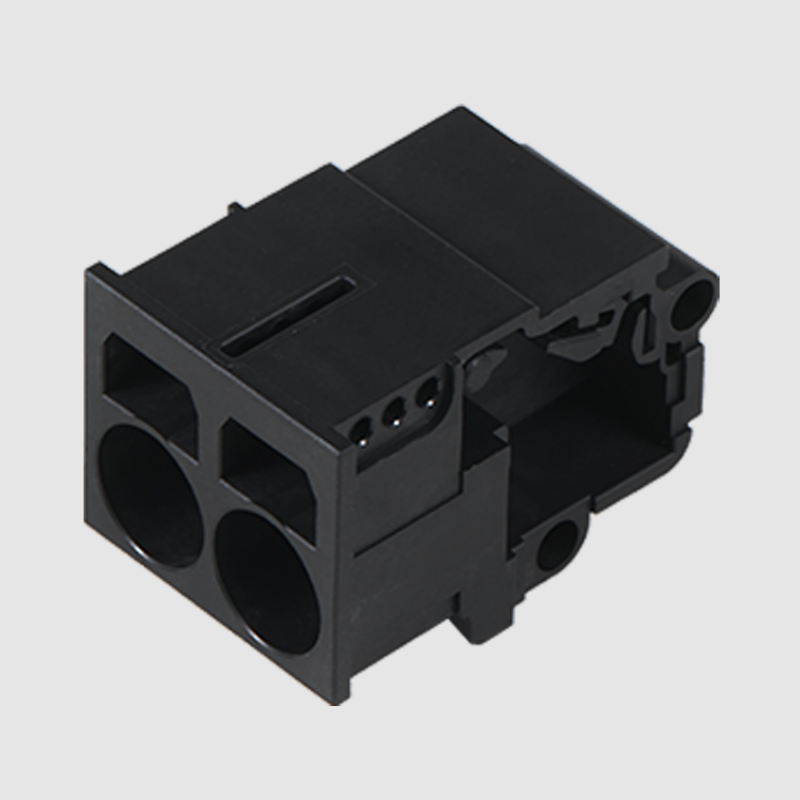
In the competitive landscape of modern manufacturing, the ability to produce unique and high-quality products is crucial for businesses to stand out. One key factor that has revolutionized the industry is the use of customized production moulds. These specialized tools have become indispensable in enabling manufacturers to create products that meet specific design requirements, ensuring both precision and efficiency in the production process.
Customized production moulds are designed to meet the unique specifications of a particular product. Unlike standard moulds, which are mass-produced for general use, customized moulds are tailored to fit the exact dimensions and design features of a specific item. This level of customization allows manufacturers to produce products with intricate details and complex geometries, which would be difficult or impossible to achieve with standard moulds.
One of the primary benefits of customized production moulds is the ability to enhance product quality. By precisely matching the design of the product, customized moulds ensure that each item produced meets the high standards of accuracy and consistency. This is particularly important in industries where product quality is paramount, such as automotive, aerospace, and medical device manufacturing. Customized moulds help to less defects and variations, resulting in products that are not only visually appealing but also functionally predominant.
Another significant advantage of customized production moulds is the potential for increased efficiency in the manufacturing process. By optimizing the design of the mould, manufacturers can reduce production time and material waste. Customized moulds can be designed to allow for faster injection cycles, quicker cooling times, and more efficient material flow. This not only speeds up the production process but also reduces costs, making it a more economically viable option for businesses.
The use of customized production moulds also supports innovation in product design. Manufacturers can experiment with new and complex designs without the constraints imposed by standard moulds. This flexibility encourages creativity and allows companies to develop products that differentiate them from their competitors. Customized moulds can accommodate unique shapes, sizes, and features, enabling the production of innovative and cutting-edge products that meet the evolving needs of consumers.
In addition to enhancing product quality and efficiency, customized production moulds contribute to sustainability efforts in manufacturing. By reducing material waste and optimizing the production process, customized moulds help to less the environmental impact of manufacturing operations. This aligns with the growing trend towards sustainable production practices and helps businesses to meet environmental regulations and consumer expectations.
The production of customized moulds is a highly specialized process that requires advanced engineering and manufacturing expertise. Skilled professionals use computer-aided design (CAD) and computer-aided manufacturing (CAM) software to create detailed and precise mould designs. These designs are then used to manufacture the moulds using advanced techniques such as CNC machining and 3D printing. The result is a high-quality, customized mould that meets the exact specifications of the product.
Customized production moulds are playing a vital role in driving innovation and efficiency in modern manufacturing. By enabling the production of high-quality, unique products, customized moulds are helping businesses to stand out in a competitive market. The benefits of increased efficiency, enhanced product quality, and support for sustainability make customized production moulds an essential tool for manufacturers. As technology continues to advance, the capabilities of customized moulds will only continue to grow, offering even greater opportunities for innovation and efficiency in the manufacturing sector.